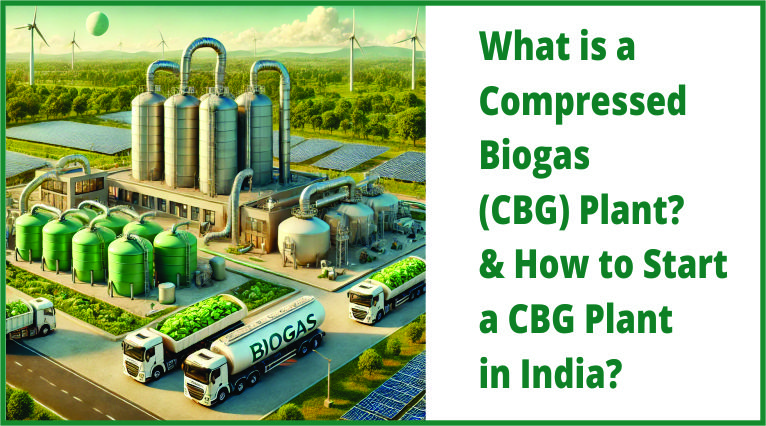
What is a Compressed Biogas (CBG) Plant and How to Start a CBG Plant in India ?
What is a Compressed Biogas (CBG) Plant and How to Start a CBG Plant in India?
Introduction
Compressed Biogas (CBG) is emerging as a key player in India’s renewable energy landscape. With abundant organic waste, government incentives, and rising demand for cleaner fuels, starting a CBG plant presents a lucrative business opportunity.
This blog will explain what a CBG plant is, how it works, and a step-by-step guide to setting up a CBG plant in India.
What is a CBG Plant?
A Compressed Biogas (CBG) Plant is a facility that processes organic waste—such as agricultural residue, grass, cattle dung, food waste, and municipal solid waste—to produce biogas, which is then purified and compressed into a renewable fuel similar to Compressed Natural Gas (CNG).
Key Features of CBG
✅ High methane content (over 90%)
✅ Can replace CNG and LPG
✅ Reduces greenhouse gas emissions
✅ Supports waste management and sustainable energy generation
CBG is used in transportation, industries, power generation, and cooking, making it a high-demand green energy solution.
Government Support for CBG in India
The Indian government actively promotes CBG plants under various schemes, including:
Sustainable Alternative Towards Affordable Transportation (SATAT) Initiative
- Launched by Ministry of Petroleum & Natural Gas.
- Encourages entrepreneurs to set up CBG plants and supply fuel to Oil Marketing Companies (OMCs).
GOBAR-Dhan Yojana
- Promotes waste-to-energy projects in rural areas.
- Provides subsidies and financial support for setting up biogas plants.
MNRE Biogas Programme
- Offers Central Financial Assistance (CFA) to support biogas projects.
- Provides incentives for power generation and thermal applications.
State-Level Subsidies
- Some states provide additional financial assistance to encourage CBG production.
- Gujarat: Subsidies Available for CBG Plants in Gujarat
Benefits of Setting Up a CBG Plant in India
✔ Abundant Feedstock: Agricultural waste, cattle dung, and municipal waste are widely available.
✔ Government Incentives: Subsidies, bank loans, and fiscal benefits reduce financial burden.
✔ Growing Market Demand: Rising need for clean fuels in transport, industries, and gas distribution.
✔ Multiple Revenue Streams: Sell CBG, organic fertilizer, and carbon credits for long-term profits.
Step-by-Step Guide to Start a CBG Plant in India
Step 1: Conduct a Feasibility Study
Before investing, conduct a feasibility study to evaluate:
- Feedstock availability (agriculture waste, animal dung, municipal waste, etc.).
- Potential buyers (OMCs, industries, transport companies).
- Government subsidies & incentives.
- Land requirement (based on plant capacity).
- Capital investment & funding options.
Step 2: Choose a Suitable Location
- Select land close to feedstock sources to minimize transport costs.
- Ensure good road connectivity for CBG distribution.
- Check for regulatory permissions and environmental approvals.
Step 3: Obtain Necessary Licenses and Approvals
- Pollution Control Board (PCB) Clearance: Approval from the State Pollution Control Board (SPCB).
- Industry Registration: Register as an MSME or startup for additional benefits.
- Fire & Safety Clearance: Ensure compliance with safety regulations.
- Oil Marketing Company (OMC) Agreement: Secure a Letter of Intent (LOI) for CBG sale to OMCs like IOCL, BPCL, HPCL.
- Power & Water Connections: Essential utilities for plant operation.
Step 4: Secure Funding and Apply for Subsidies
Starting a CBG plant requires significant investment. Explore the following options:
A. Government Subsidies & Incentives
- GOBAR-Dhan Yojana: ₹37,000 per unit for biogas plants.
- MNRE Biogas Programme: ₹35,000-45,000 per kW for power generation projects.
- State-Specific Subsidies: Check respective state government policies.
B. Bank Loans
- SBI, SIDBI, NABARD, Bank of Baroda offer project loans for CBG plants.
- Interest rates typically range from 8-12%, with government backing available.
C. Private Investment & VC Funding
- Approach venture capitalists, renewable energy investors, or impact funds for financing.
Step 5: Design and Construct the CBG Plant
A. Procure Machinery and Equipment
- Anaerobic digesters
- Biogas purification & upgrading unit
- Gas storage tanks & compression unit
- Pipeline & dispensing system
- Power backup & monitoring system
B. Build Infrastructure
- Construct digestion tanks, storage units, and processing facilities.
- Set up electrical, water, and safety systems.
Step 6: Establish Supply Chain & Market CBG
- Tie up with Oil Marketing Companies (OMCs) for long-term supply agreements.
- Partner with industries, transport companies, and gas distributors for bulk sales.
- Sell by-products like organic fertilizer (bio-slurry) to farmers.
Step 7: Begin Production & Optimize Operations
- Ensure regular feedstock supply for continuous production.
- Monitor plant efficiency and optimize operations.
- Conduct quality control to maintain high methane content in CBG.
Investment Required for a CBG Plant in India
The cost depends on capacity and scale:
Plant Size | Investment (₹) | Feedstock Processing Capacity | CBG Production Capacity (kg/day) |
---|---|---|---|
Small (2-5 TPD) | ₹2-5 Crore | 2-5 Tons Per Day | 150-300 kg/day |
Medium (5-20 TPD) | ₹10-25 Crore | 5-20 Tons Per Day | 500-2000 kg/day |
Large (20+ TPD) | ₹25-50 Crore | 20+ Tons Per Day | 2500+ kg/day |
Cost Breakdown
Component | Small (₹ Cr) | Medium (₹ Cr) | Large (₹ Cr) |
---|---|---|---|
Land & Civil Work | 0.50 – 1.00 | 1.50 – 3.00 | 3.00 – 6.00 |
Plant & Machinery | 0.80 – 1.50 | 2.50 – 5.00 | 6.00 – 12.00 |
Digester & Purification | 0.50 – 1.00 | 2.00 – 4.50 | 4.00 – 8.00 |
Storage & Compression | 0.30 – 0.50 | 1.00 – 2.50 | 2.00 – 4.50 |
Pipeline & Dispensing | 0.30 – 0.50 | 1.00 – 2.00 | 2.00 – 4.00 |
Working Capital | 0.40 – 1.00 | 1.50 – 3.00 | 4.00 – 8.00 |
Miscellaneous | 0.20 – 0.50 | 1.00 – 2.50 | 3.00 – 5.00 |
Total Investment | ₹2-5 Cr | ₹10-25 Cr | ₹25-50 Cr |
The cost breakup for CBG plant setup is based on standard industry parameters, project scale, technology, and operational requirements. The following assumptions have been considered:
1. General Assumptions
✅ Land Requirement:
- Small Plant (2-5 TPD) → 1-2 acres
- Medium Plant (5-20 TPD) → 2-5 acres
- Large Plant (20+ TPD) → 5-10 acres
- Land cost is not included in the estimates (varies by location).
✅ Feedstock Availability & Cost:
- Agricultural waste, municipal waste, cattle dung, or food waste.
- Assumed feedstock cost: ₹500-₹1,500 per tonne (depends on waste type).
✅ Technology Used:
- Anaerobic Digestion Process with modern purification and upgrading systems.
- Automated gas storage and compression units.
✅ Project Implementation Timeline:
- Small Plant: 6-12 months
- Medium Plant: 12-18 months
- Large Plant: 18-24 months
✅ Production & Utilization:
- CBG Yield: 50-55 kg per tonne of feedstock.
- Digestate (by-product) utilized for organic fertilizer sales.
2. Cost Breakup Assumptions
Cost Component | Assumptions |
---|---|
Land & Civil Construction | Cost includes site preparation, foundation, roads, and storage facilities. |
Plant & Machinery | Includes anaerobic digesters, gas purification units, compressors, and automation systems. |
Digester & Purification Unit | Includes high-efficiency digesters and membrane purification systems for methane enrichment. |
Storage & Compression Unit | Covers high-pressure storage tanks, gas bottling system, and booster compressors. |
Pipeline & Dispensing System | Cost assumes 1-5 km pipeline for industrial/commercial gas supply. |
Electrical & Utility Setup | Includes power backup, control panels, and automation systems. |
Working Capital | Covers raw material procurement, labor, and operational expenses for 6 months. |
Miscellaneous & Contingency | Assumed 10-15% of total project cost for unforeseen expenses. |
3. Expected Revenue & Profitability
Plant Size | Daily CBG Production | Annual Revenue from CBG (₹) | Additional Revenue from Fertilizer (₹) | Total Annual Revenue (₹) |
---|---|---|---|---|
Small (2-5 TPD) | 150-300 kg | ₹2-4 crore | ₹0.5-1 crore | ₹2.5-5 crore |
Medium (5-20 TPD) | 500-2000 kg | ₹6-20 crore | ₹2-6 crore | ₹8-26 crore |
Large (20+ TPD) | 2500+ kg | ₹25+ crore | ₹8-12 crore | ₹30-40 crore |
4. Operational Cost Assumptions
Expense Type | Estimated Cost (₹/year) |
---|---|
Feedstock Procurement | ₹50 lakh – ₹5 crore |
Power & Utilities | ₹10 lakh – ₹1 crore |
Labor & Maintenance | ₹20 lakh – ₹2 crore |
Transportation & Logistics | ₹10 lakh – ₹50 lakh |
Marketing & Sales | ₹5 lakh – ₹25 lakh |
Miscellaneous Expenses | ₹5 lakh – ₹1 crore |
Key Considerations
📌 Economies of Scale: Larger plants benefit from lower per-unit costs due to bulk production.
📌 Government Incentives: CBG plants receive capital subsidies, reducing overall investment burden.
📌 CBG Pricing: Market rates for CBG range from ₹50-₹75 per kg, depending on buyers.
🔄 Choosing the Right Subsidy Scheme for Your CBG Plant
Before you proceed with setting up your CBG plant, it’s crucial to select the right government support scheme. The Indian government currently promotes CBG through three key programmes:
BAM Scheme (for innovative & R&D-based projects)
SATAT Scheme (for market linkage with OMCs)
Waste to Energy Programme (for capital subsidy up to ₹10 Cr)
💡To help you decide the most suitable option for your project, we’ve prepared a detailed comparison.
👉 Read here: CBG Subsidy Scheme Comparison – BAM vs SATAT vs Waste to Energy
Conclusion
Setting up a Compressed Biogas (CBG) plant in India is a profitable and sustainable business opportunity. With government support, abundant biomass, and rising demand for clean energy, now is the best time to invest in CBG production.
If you need assistance with project reports, funding, or government approvals, Adroit Corporation can help.
📞 Contact Us: 8734010101
📧 Email: sales@adroitcorporation.in
Let’s build a greener and more sustainable India with Compressed Biogas (CBG)! 🚀🌿